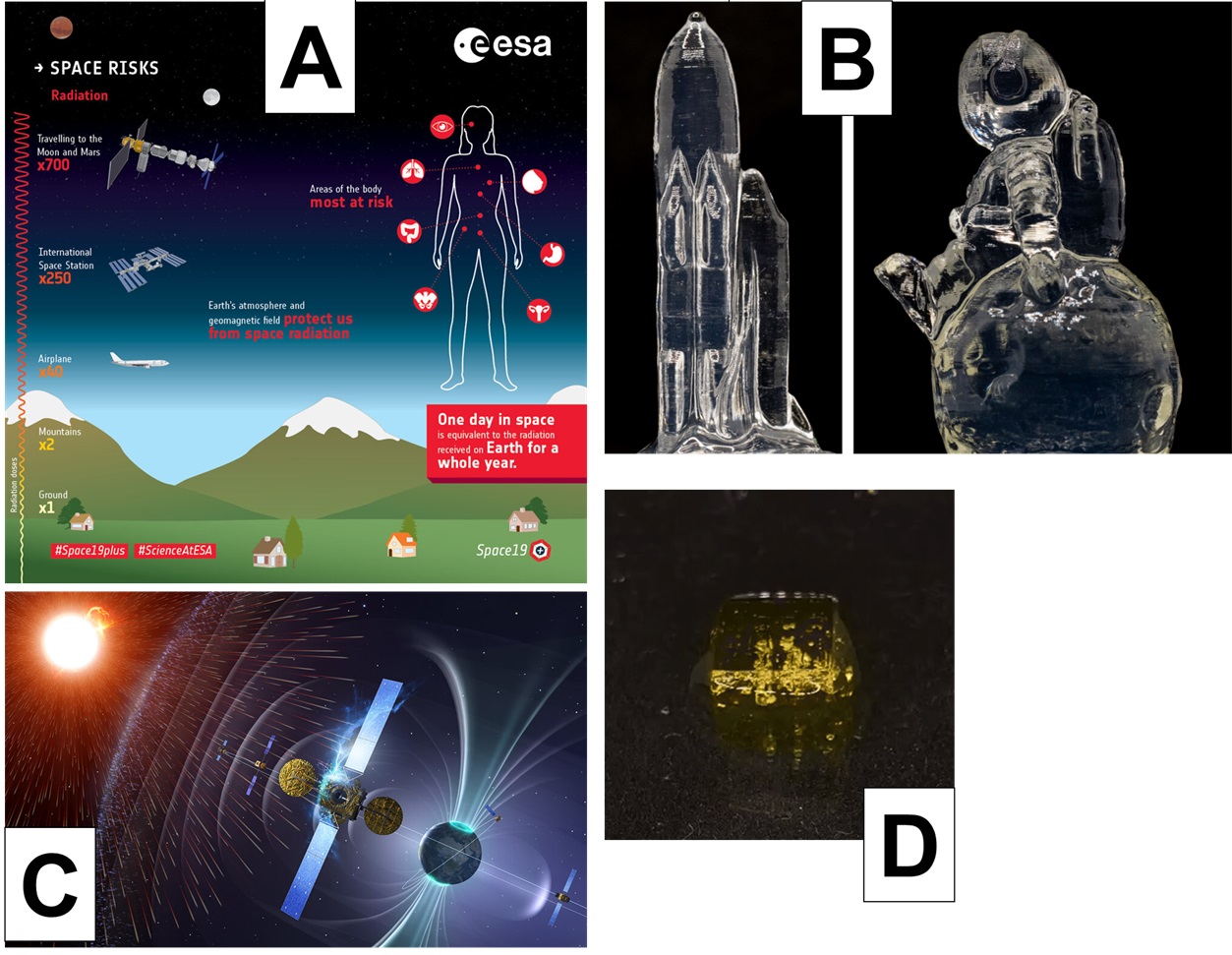
6 Feb 202
Space is not the safest place to be. During spaceflight, both devices and humans risk exposure to high levels of radiation. Without sufficient protection, instruments would malfunction, and astronauts might face serious health risks. A team of researchers from Ghent University in Belgium are testing the potential of 3D-printed hydrogels – materials that can soak up large amounts of water – to serve as highly-effective radiation shields.
Space is anything but empty – powerful streams of high-energy particles, moving nearly at the speed of light, are thrown off by the Sun during solar flares or find their way to our galaxy from powerful explosions in deep space.
On Earth, we are shielded from most of the cosmic radiation by our planet’s atmosphere and magnetic field. In just one day beyond these protective layers, astronauts are exposed to the equivalent of radiation received on Earth in a whole year. Explorers venturing even farther, for example during future missions to Mars, will need another way to protect themselves from these harmful rays.
Studies have identified water as one of the materials best suited for radiation shielding. It is relatively dense and contains lots of hydrogen atoms, which interact with incoming radiation particles and slow them down. However, a free-flowing water-based radiation protection system has its challenges.
Bulky containers embedded into spacesuits could limit astronauts’ movement, unequal water distribution would lead to incomplete protection, and the water could leak out if the container is punctured – which can be especially dangerous in an environment full of electronics.
In a follow-up study to a successful Discovery activity, a research team from the Polymer Chemistry and Biomaterials Group (PBM) at Ghent University in Belgium are exploring the use of superabsorbent polymers (SAPs) as an alternative material for radiation shields, safer and more effective than water alone.
SAP is a material capable of absorbing up to several hundred times its weight in liquid, just like ‘grow monster’ toys that expand when submerged in water. In their swollen state, SAPs are referred to as ‘hydrogels’.
“The beauty of this project is that we are working with a well-known technology,” explains Lenny Van Daele. “Hydrogels are found in many things we use every day, from contact lenses to diapers and sanitary products. Our research group has experience with applications in the medical field – using hydrogels as a soft implantable material to repair damaged tissues and organs.”
Hydrogels’ ability to retain water makes them a suitable radiation protection for habitats, as well as in spacesuits used for extravehicular activities (EVAs). The water retained in a hydrogel is not free-flowing, which allows for equal distribution and protection. This also means the water would not leak out if the patch was punctured, giving astronauts enough time to get to safety.
“The material could also potentially be applied to uncrewed missions – in radiation shields for spacecraft, or as water reservoirs once we have optimised the method of retrieving water from the hydrogel,” adds Malgorzata Holynska of European Space Agency’s Materials, Environments and Contamination Control Section.
“The superabsorbent polymer that we are using can be processed using multiple different techniques, which is a rare and advantageous quality amongst polymers,” adds Manon Minsart. “Our method of choice is 3D printing, which allows us to create a hydrogel in almost any shape we want."
Lead of the project Peter Dubruel comments: “There is a constant search for lightweight radiation protection materials. In our Discovery activity we successfully demonstrated that hydrogels are safe to use under space conditions. In this follow-up project, we are applying different techniques to shape the material into a 3D structure and scale up the production process, so that we can come a step closer to industrialisation.”
[Image]
(A) Space risks – Radiation
(B) 3D-printed hydrogel space shuttle and astronaut on the Moon
(C) Space radiation
(D) Timelapse of hydrogel swelling, showing a 1.5-hour-long process in 6 seconds