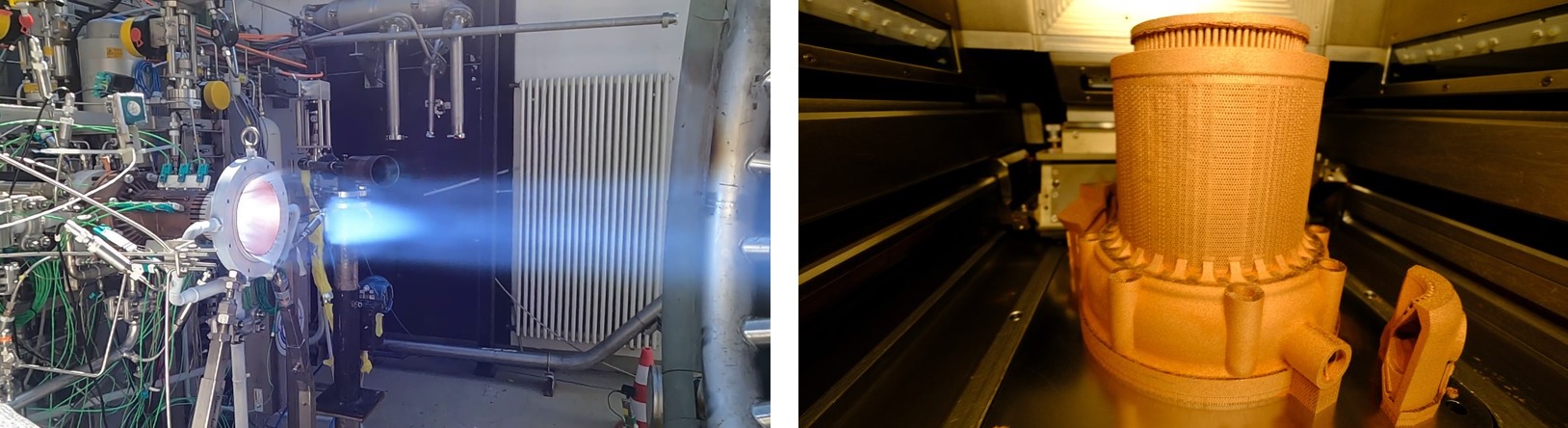
2023 年 8 月 2 日
- 航天市場的競爭對發射器技術提出了新的要求,特別是在降低成本和可重複使用性方面。
- DLR 3D-LoCoS 項目表明增材製造可以在未來的太空推進中發揮重要作用。
- 3D打印的燃燒室成功通過蘭波爾德斯豪森P8歐洲研究和技術測試台的熱運行測試。
- 重點領域:太空旅行、增材製造、數字化、人工智能
最大安全性、高性能、長使用壽命——這些是太空推進系統必須滿足的重要要求。當前的驅動技術已經能夠做到這一點。但是降低成本和可重用性又如何呢?這些是具有競爭力的重要標準。德國航空航天中心 (DLR) 的科學家們正在“3D-LoCoS - 低成本空間部件 3D 打印”項目中密切關注這些參數。重點是金屬增材製造(即3D打印工藝)的進一步開發和應用。這意味著可以更經濟、更快速地生產空間組件的技術演示器。
降低成本作為太空旅行的競爭標準
“新的製造工藝是提高成本效率的關鍵,並為可重複使用的載體技術鋪平了道路,”博士強調說。Jan Haubrich,德國航天中心材料研究所的項目經理。在3D-LoCoS項目中,來自德國航天中心設計與結構技術研究所、空間推進研究所、軟件技術研究所和材料研究所的跨學科團隊共同努力。目的是通過增材製造工藝“激光粉床融合”(LPBF) 擴大可能性。LPBF 粉末床工藝適用於特別複雜或金絲細工的結構。
“我們設計並開發了一種具有特殊再生冷卻概念的燃燒室,特別適用於增材 LPBF 製造工藝,”Dr. 來自 DLR 太空推進研究所的德米特里·蘇斯洛夫 (Dmitry Suslov)。銅、鉻和鋯石的合金使燃燒室的材料具有高導熱性和耐溫性。
P8試驗台上的新製造工藝
在P8 研究和技術測試台上進行熱運行測試在蘭波爾德斯豪森,推力為 25 千瓦的 3D 打印燃燒室的設計和製造過程均取得了成功。“通過六次熱運行測試,我們能夠展示使用 3D 打印生產的燃燒室的新設計和功能的巨大潛力,”Dmitry Suslov 說道。“現在我們希望盡快將這項技術推向工業應用。該測試系列證明增材製造為發動機部件的設計和製造提供了廣泛的應用範圍。”整個項目還使用了基於人工智能(AI)的創新設計方法——從燃燒室的設計到測試在測試台上。
金屬增材製造作為一項創新
Jan Haubrich 表示:“增材製造工藝允許以完全不同的方式製造部件,與大多數其他金屬加工工藝相比,它是一項相對年輕的技術。”他指出了良好的未來前景:“特別是對於複雜的設計,部件可以打印更多便宜又快捷”。然而,增材製造材料的行為與傳統加工材料不同。因此,需要進一步的測試和進一步的技術開發。後續項目是利用人工智能進一步將銅燃燒室開發成飛行硬件。同時,合作項目要加強向產業轉移。
通往燃燒室的道路
事實上,燃燒室將使用 3D 打印技術生產,這一事實在設計階段就已經成為焦點。例如,因為 LPBF 流程會產生影響設計的新要求。氣密性、幾何精度和表面粗糙度等性能對於設計具有決定性作用。出於這個原因,研究人員首先檢查了新的燃燒室設計是否可以3D打印。LPBF 工藝和製造策略通過材料測試和原型進行了驗證。這樣就可以在生產系統上一體式地製造燃燒室,該生產系統的特殊尺寸使得可以一體式地生產長度超過60厘米的燃燒室。